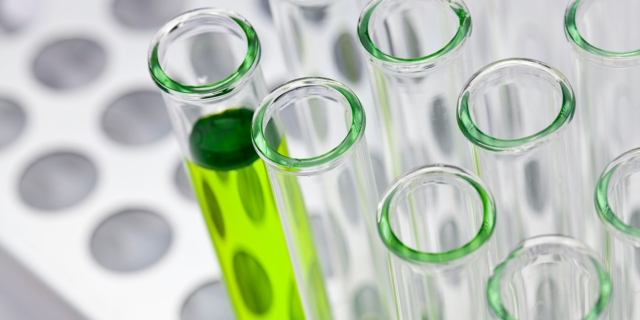
The textile Industry can be a pioneer in the Eco-friendly effort.
Let’s start with some numbers regarding the Textile Industry in order to have a better understanding of the impact that textile recycling can have. The
Let’s start with some numbers regarding the Textile Industry in order to have a better understanding of the impact that textile recycling can have. The
InformEX is an annual tradeshow and conference held for companies involved in the specialty chemical and custom chemical manufacturing markets. Geared towards anyone from production
In an ever-changing manufacturing environment, a continuous safety culture is extremely important. One way to foresee and hopefully prevent accidents is through the Hiyari Hatto
ISPO is the biggest gathering of sportswear and the outdoor industry in the world. The exposition features over 150 events from technical discussions to a
In the past few years, customers have been seeking a more environmental friendly life style and this trend has influenced the textile industry in many
AATCC is having its 2015 International Conference in Savannah, GA on March, 25 and 26 2015. NICCA USA has been selected to present its latest
In the manufacturing industry, a lot of tools are used to implement process improvement, monitor production, and maintain safe operations. Some of these
The manufacturing of chemicals is an astringent process. It needs a strong team in the plant and in the lab to be able to assure
The textile industry is always trying to become more environmental friendly. It is a major concern from chemical manufacturers to the brands to provide consumers
Hospital Associated Infections (HAIs) are a major issue in Hospitals worldwide. In America about 1 out of 25 patients who stay in a hospital will
The quality of NICCA USA products is well-known in the Industry and, to keep producing high performing agents, the Engineering and Maintenance teams of NICCA
The main goal of NICCA USA is to provide customers with high quality products. In order to achieve this not always easy goal, all the
Dyeing auxillaries and functional finishes
PFPE oils for specialty greases and vacuum oil
Finishes and coatings for nonwovens and filters
Specialty textile, nonwoven, paint, and more solutions
Anti-soils, stainblockers, and anti-stats
Resins, PTSA catalysts, and special topcoats
PTSA catalysts and toll manufacturing